Light Weight Aluminum Casting Proficiency: Strategies and Tools for Exceptional Outcomes
Grasping the art of aluminum casting requires a fragile equilibrium of accuracy, technique, and the usage of specialized tools. From the initial phases of thawing the aluminum to the intricate process of mold and mildew preparation and putting, each step plays a critical role in attaining exceptional results. As we check out the elaborate methods and tools associated with aluminum casting proficiency, one can not neglect the significance of sophisticated pouring and cooling down methods that can elevate the final result. Stay tuned to reveal the important devices and finishing touches that pave the way for impeccable light weight aluminum spreadings.

Importance of Appropriate Melting Techniques
Utilizing precise temperature control during the melting process is extremely important in making sure the top quality and honesty of aluminum castings. The melting of light weight aluminum is a crucial action in the casting procedure, as it directly affects the final homes of the casted parts. Correct melting techniques are necessary to accomplish the preferred metallurgical structure, mechanical residential properties, and surface area finish of the aluminum elements.
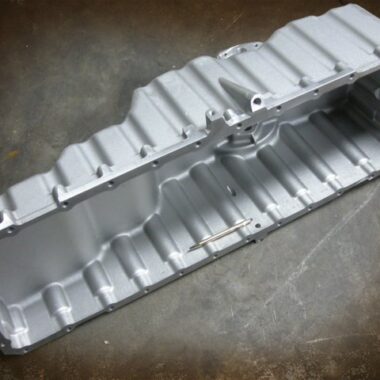
Additionally, monitoring and changing the thaw temperature throughout the process help protect against getting too hot, which can trigger grain development and influence the general quality of the aluminum casting. Following accurate melting strategies not only enhances the top quality of the end product yet also boosts the efficiency and cost-effectiveness of the spreading procedure.
Crucial Mold And Mildew Preparation Steps
Correct preparation of molds is a fundamental facet in the aluminum spreading procedure, making sure the successful duplication of detailed information and dimensions in the last casted elements. The vital mold prep work steps begin with selecting the ideal molding product, such as sand or financial investment spreading materials, based upon the details of the component and desired surface. Before pouring the liquified aluminum, the mold cavity must be thoroughly cleansed and dried out to stop problems in the spreading. Furthermore, using mold coatings can help boost surface finish and prolong mold and mildew life.
Moreover, correct gating and risering style are vital in mold and mildew preparation to guarantee sound castings with marginal flaws like porosity and contraction. The gating system promotes the circulation of molten metal right into the mold and mildew dental caries, while risers aid protect against shrinkage by providing added molten metal as the casting solidifies. Cautious consideration of these facets throughout mold and mildew prep work substantially adds to the quality and honesty of the last light weight aluminum cast parts.
Advanced Pouring and Cooling Approaches
Applying innovative pouring and cooling approaches is crucial in maximizing the light weight aluminum spreading process for boosted effectiveness and high quality outcomes. Making use of strategies such as vacuum spreading can significantly minimize porosity in the last item, causing enhanced mechanical residential properties. By evacuating the air from the mold and mildew tooth cavity prior to putting, the threat of gas entrapment is lessened, causing a denser and more structurally sound spreading.
Additionally, utilizing controlled air conditioning approaches, such as water quenching or air cooling, can affect the product's microstructure and mechanical features (about aluminum casting). Fast cooling can help accomplish finer grain frameworks and improved mechanical residential or commercial properties, making the actors light weight aluminum better for applications requiring high strength and resilience
Additionally, executing directional solidification methods, where the casting strengthens gradually from one end to one more, can help alleviate interior flaws and enhance overall part honesty. By very carefully taking care of the temperature level differentials throughout solidification, the development of shrinkage porosity and these details warm rips can be decreased, leading to higher quality spreadings with boosted mechanical efficiency.
Important Tools for Aluminum Casting
Enhancing the effectiveness and quality end results of aluminum casting processes depends heavily on the application of certain devices designed to optimize various aspects of the spreading operation. One essential device for aluminum casting is the crucible. Crucibles are containers constructed from materials like clay-graphite or silicon carbide that withstand the heats required for melting light weight aluminum. Crucibles can be found in different sizes to accommodate various spreading volumes and are essential for melting and pouring the molten light weight aluminum.
One more essential tool is the mold and mildew. Mold and mildews can be made from materials like metal, sand, or plaster and are made use of to shape the molten aluminum right into the desired form. about aluminum casting. Correct mold and mildew style and products are essential for attaining exact spreading dimensions and surface area coatings
Along with molds and crucibles, a heating system is a basic device for aluminum spreading. Heating systems heat the steel to its melting factor, ensuring it is in a state all set for casting. Essential for maintaining regular temperature levels and guaranteeing the light weight aluminum continues to be molten, heating systems are available in different kinds, such as electric, gas, or induction heating systems, each with its benefits for certain casting demands.
Ending Up Touches and Quality Checks
Upon completing the spreading process, thorough focus to finishing touches and extensive high quality checks is paramount to guarantee the stability and accuracy of the light why not check here weight aluminum components - about aluminum casting. Completing touches include the removal of any excess product, such as flash, gating systems, or harsh sides, to achieve the desired last shape and surface top quality. This step commonly consists of processes like grinding, sanding, or fired blasting to improve the appearance and appearance of the actors parts
Quality checks are then carried out to validate that the parts satisfy the specific requirements and standards. These checks may entail dimensional evaluations utilizing accuracy tools like calipers or coordinate determining equipments to guarantee precision. In addition, non-destructive testing techniques such as ultrasonic screening or X-ray evaluation can be employed to discover any internal issues that might compromise the architectural stability of the components.
Verdict
In verdict, grasping aluminum spreading strategies and making use of the right devices is crucial for accomplishing outstanding outcomes. Proper melting strategies, mold preparation, putting and cooling down techniques, along with finishing touches and top quality checks are vital actions in the spreading procedure. By adhering to these actions thoroughly and utilizing the suitable tools, one can ensure a successful and high-quality aluminum casting manufacturing.
As we explore the intricate techniques and tools involved in aluminum spreading proficiency, one can not neglect the significance of sophisticated pouring and cooling down techniques that can raise the last outcome.Correct prep work of molds is a fundamental aspect in the light weight aluminum casting procedure, making certain the successful replication of detailed information and dimensions in the final casted elements. Prior to pouring the liquified light weight aluminum, the mold and mildew cavity must be carefully cleaned and dried to prevent problems in the spreading.Enhancing the performance and top quality outcomes of light weight aluminum spreading procedures depends greatly on the application of particular devices developed to maximize different aspects of the spreading procedure.In addition to mold and mildews and crucibles, a furnace is a fundamental tool for light her response weight aluminum casting.
Comments on “Advancement Unleashed: Innovations About Aluminum Casting”